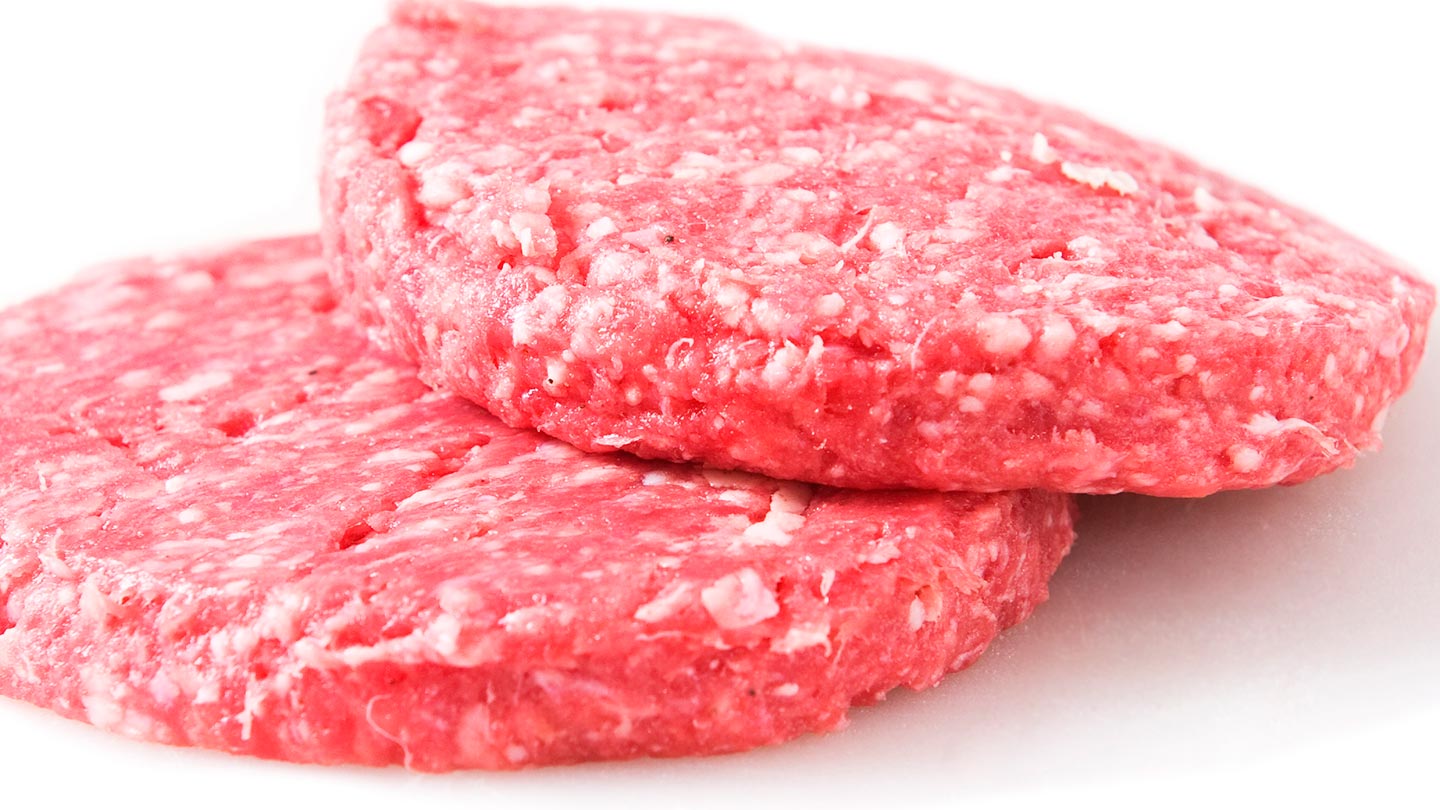
800-654-4567 | Contact Us
A warm mixed product fails to hold its shape and can stick to the forming plate. This results in unnecessary waste and rework. A common solution is to add ice water, dry ice, or frozen ingredients during the mixing or blending step. But this is not precise and can be time consuming or even unhygienic. This often fails to achieve the desired texture and temperature for your formed product. A popular alternative is to fit a liquid nitrogen or CO₂ injection system to the mixer or blender.
Food Applications Specialist, Americas
How can I improve factory output of a mix of frozen products?
Air Products gases, typically provided in gaseous and liquid form, enable customers in a wide range of industries to improve their environmental performance, product quality, and productivity.
Our experienced applications teams across the globe can use their industry and application knowledge to provide you with a compressed or liquid carbon dioxide supply and technology solution to meet your unique needs.
Useful as a gas, for its inert properties, and as a liquid for cooling and freezing. Virtually any industry can benefit from its unique properties to improve yields, optimize performance and make operations safer.
Delivered by truck and stored on your site either as a liquid in cryogenic tanks or as a gas in high-pressure tubes based on your volume, desired pressure, purity level, flow rate, and operating pattern.