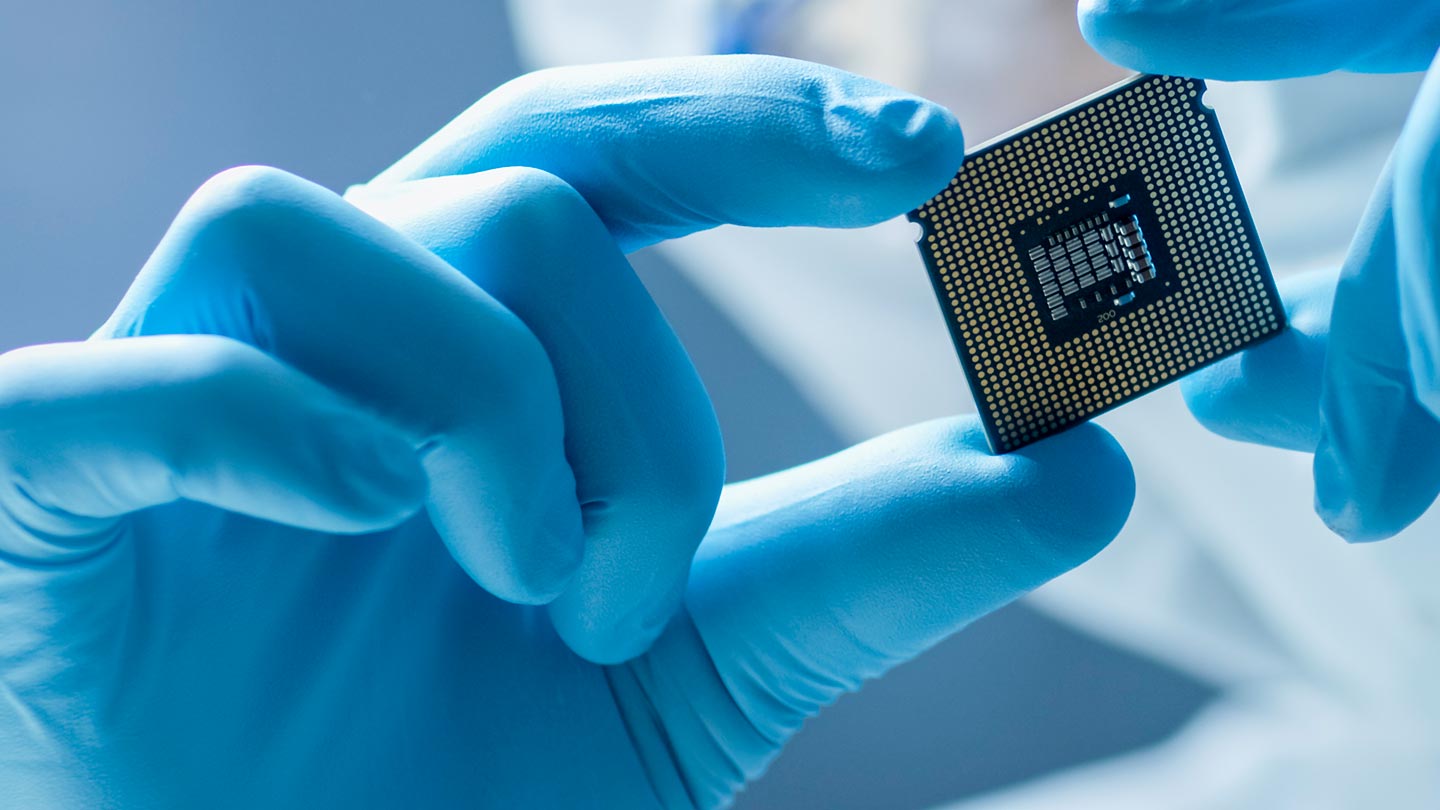
800-654-4567 | Contact Us
The electronics packaging and assembly industry is constantly adjusting to satisfy the requirements of the newest generation of semiconductors. Smaller footprint device sizes, 2.5D and 3D TSV packaging are just some of the changes that have occurred.
With these changes come challenges to the manufacturing process, so how to use and control of nitrogen or hydrogen-based atmospheres is critical to achieve the best performance.
Air Products’ expertise, technologies and gas supply advantages can provide improved performance and up-time, while reducing defects and total cost of ownership for your integrated circuit board assembly and test processes.
Air Products gases, typically provided in gaseous and liquid form, enable customers in a wide range of industries to improve their environmental performance, product quality, and productivity.
Compressed argon gas and liquid argon in a variety of purities and in various modes of supply around the world thanks to our network of storage and transfill facilities.
Our experienced applications teams across the globe can use their industry and application knowledge to provide you with a compressed or liquid carbon dioxide supply and technology solution to meet your unique needs.
An inert gas for cryogenic, heat transfer, shielding, leak detection, analytical and lifting applications
Valued for its reactive and protective properties, and used by many industries such as electronics, foods, glass, chemicals, refining and more can benefit from its unique properties to improve quality, optimize performance and reduce costs.
Useful as a gas, for its inert properties, and as a liquid for cooling and freezing. Virtually any industry can benefit from its unique properties to improve yields, optimize performance and make operations safer.
In addition to its use as a respiratory gas for healthcare applications, its strong oxidizing properties benefit many industries by improving yields, optimizing performance, lowering costs and reducing carbon footprint compared to other fuels.
We are experiencing poor underfill flow in our flip chip assemblies. What is the possible cause and is there a solution that can be implemented to improve our underfill process?
Poor underfill flow is a common concern in flip chip assembly and is due to several issues. The predominate problem is contaminates left behind post reflow assembly. The primary contaminate is flux residue. Although you may clean the assembly post reflow, the likelihood of flux left behind is high. Most fluxes will polymerize during the reflow process in air or high O₂ ppm level (>500 O₂ ppm). Current cleaning processes may not be efficient enough to remove all the residue under the flip chip. The key is to use an inert atmosphere, such as nitrogen or argon, to eliminate high O₂ levels. The high O₂ levels will cause the flux to polymerize and be difficult to clean.
Best process practice is to use an O₂ ppm level of around 100 ppm. This will give you two benefits: (1) reduce the chance of flux polymerization and allow for good results post cleaning and (2) allow the flux to stay active longer increasing the fluxing properties to insure good wetting and provide a reliable solder joint.
Air Products can assist you in evaluating your processes and offer solutions to your concerns in this area.